Benchmark for single-stage shredding
UNTHA shredding technology GmbH has been developing and producing industrial shredders for various areas of waste recycling and resource recovery for decades. The Austrian premium manufacturer stands for high quality and reliability. The first generation of the UNTHA XR class was developed over 20 years ago. Since then, the machines and their advanced models have proven their worth over and over again, delivering outstanding performance in the cost-efficient shredding of waste wood, tyres/rubber, pulper ropes, commercial and industrial waste, and bulky waste. Innovative technology, years of experience and systematic further development make the UNTHA XR one of the best shredders on the market for particularly challenging applications and high material volumes. In addition, these shredders impress with high efficiency and attractive operating costs (€/t).
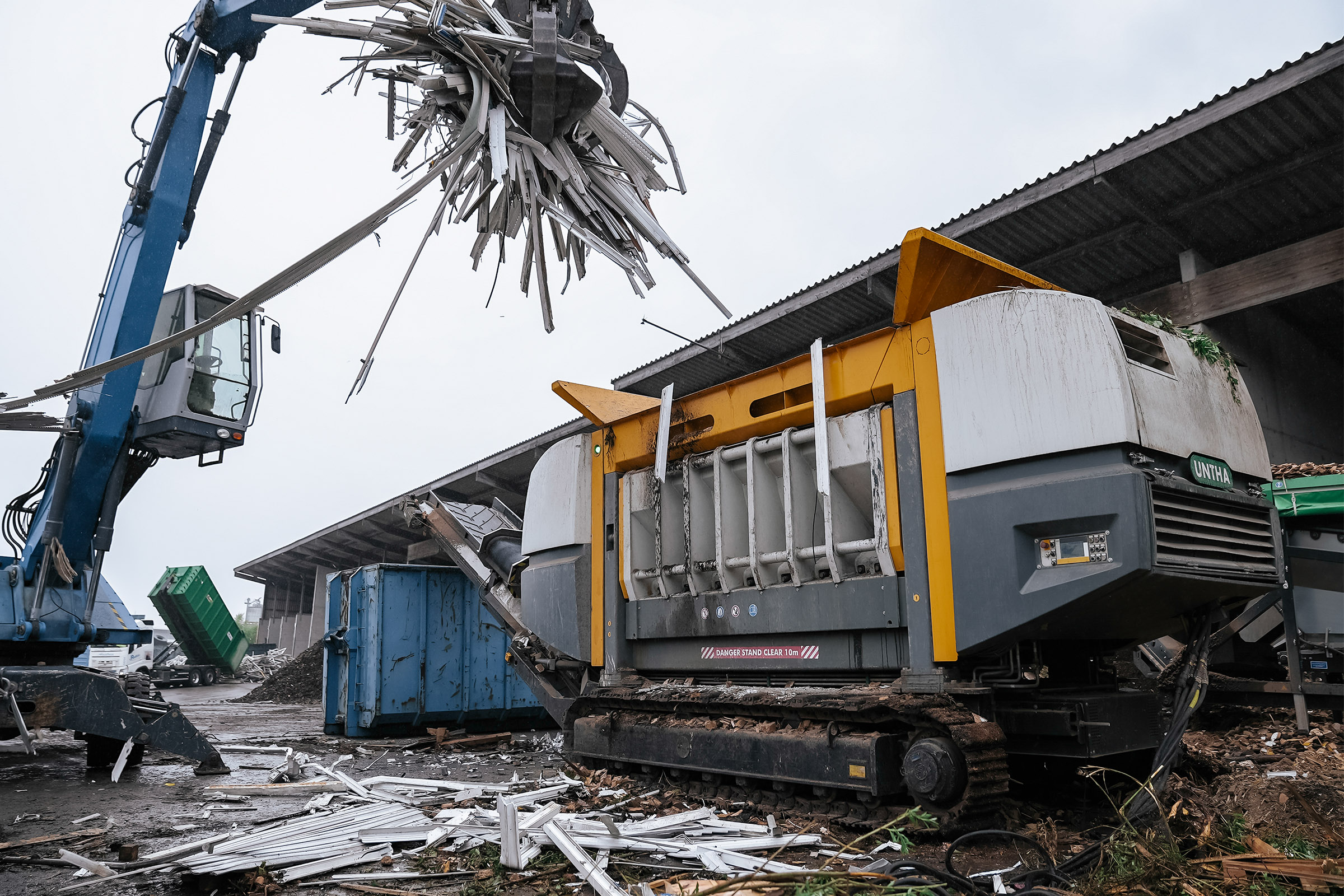
'UNTHA and the XR series stand for single-stage shredding – because we have made it a reality. And when it comes to pre- and post-shredding, our machines prove every day that true innovation starts with UNTHA. This also includes the continuous further development of our shredders based on comprehensive material tests and, above all, our customers‘ feedback. This enables us to adapt our shredders to the recycling of ever new material flows and thus to respond to developments in the industry and on the market,’ says Stefan Scheiflinger-Ehrenwerth, CIO of UNTHA shredding technology GmbH.
The XR class – the original
The shredders in the XR class are particularly powerful single-shaft machines that have been specially developed for the recycling of challenging materials. They are characterised by their economical processing of a wide range of waste and recyclable materials, as well as their high throughput and reliability. The shredders are individually adapted to the customer's requirements and configured accordingly – depending on the material (composition), input and output size, and the desired throughput.
‘XR customers particularly appreciate the flexibility and customisability of the machine. They can purchase a single-stage setup and adapt it later if needed. This means that an original pre-shredder can later be used as a mid- or post-shredder, or vice versa. The shredders can also be individually integrated into a wide range of different plants,’ explains Stefan Scheiflinger-Ehrenwerth.
Cutting units: Depending on the input material and the desired fraction size, different cutting units can be used in the shredder. The RC-cutting system was developed specially for the pre-shredding of different material flows and for high throughput rates of up to 70 t/h. The unique shape of the teeth rips and cuts at the same time, ensuring that the material is drawn in perfectly without the need for pushers. The C-cutting system is used to achieve very precise cuts and thus a particularly homogeneous and fine output material, even in a single stage. UNTHA's XC-cutting system was developed for granulating or re-shredding pre-treated materials.
Direct drive: The UNTHA Eco Power Drive is a wear-free direct drive that does not require parts such as belts or shaft stubs. This means that the full power of the synchronous motors is transferred directly to the shredding shaft via the gearbox and protective coupling. It is particularly slow-running at 5–35 rpm, which keeps dust and noise emissions as well as vibrations very low. The direct drive stands for maximum efficiency and low maintenance costs. The load-dependent speed control ensures high throughput rates and an optimal shredding process that can be adapted to the respective material.
Stationary / mobile-e: The XR class is available in 2000 mm or 3000 mm sizes and as a stationary or semi-mobile variant (mobile-e), i.e. equipped with a mobile undercarriage. Both variants are identical in design and functionality, so customers do not have to compromise on shredding performance.
Perforated screens / screen rods: The shredders can be equipped with different perforated screens or screen sticks at various distances. In cooperation with the cutting mechanism, they deliver grain sizes of 10-300 mm.
GENIUS: This digital assistance system allows the operation of the grinder to be monitored and optimised in real time. Sophisticated sensor technology is used to collect process data, and GENIUS calculates appropriate optimisation suggestions. In addition, predictive maintenance ensures that service and maintenance work is planned at an early stage. This reduces downtime and ensures smooth operation.
The perfect synergy of all these features and the robust and low-maintenance design of the XR class result in top performance, making these shredders an excellent investment with an unbeatable ROI.
Live demonstrations with the XR class
Interested parties have the opportunity to test the UNTHA XR intensively in their own operations - with their material and under real conditions - before making a purchase decision. During this test operation, UNTHA experts are on hand to provide support in order to achieve the best possible result.
The test operations are carried out with semi-mobile machines, as they can be quickly and easily brought to the prospective customers and flexibly placed there. The technology inside the shredders is the same, whether stationary or mobile-e. This means that customers always get exactly what they have tested.
Materials shredded: industrial and commercial waste, waste wood and railway lines, metal, pulper ropes, mattresses, carpets, mixed construction waste, tyres/rubber and much more.
‘We ran a test operation with the UNTHA XR3000RC mobil-e at our company for several weeks. During this time, a variety of materials, such as hard plastics, foils, bulky waste and waste wood, were shredded. Various perforated screens and machine settings were also used. We are extremely pleased with the shredder and the support provided by UNTHA,’ said Thomas Schenker, Managing Director of Schenker Industrie- und Städtereinigungs GmbH.
Find out more about UNTHA XR and watch live demos at: UNTHA XR – stationary/mobile-e
Pictures available to download (may be reprinted free of charge for press purposes, picture credits: UNTHA shredding technology GmbH) https://untha.canto.de/s/QRSJE?viewIndex=0
Picture 1: UNTHA XR3000RC mobil-e: coarse pre-shredding of commercial waste
Picture 2: UNTHA XR3000C stationary in a domestic waste recycling plant
Picture 3: UNTHA XR3000XC stationary shredding pre-treated materials