References
To showcase how a trio of UNTHA shredders have supported The Royal Mint’s ‘world-first’, multi-million-pound e-waste facility, extracting precious metals for recovery and reuse. Working with such an ambitious and high-calibre client, in collaboration with a network of engineering partners, this case study works to build authority, credibility, and trust among customers and prospects, positioning UNTHA as a key player in driving circular economy solutions and sustainable waste management in the industry.
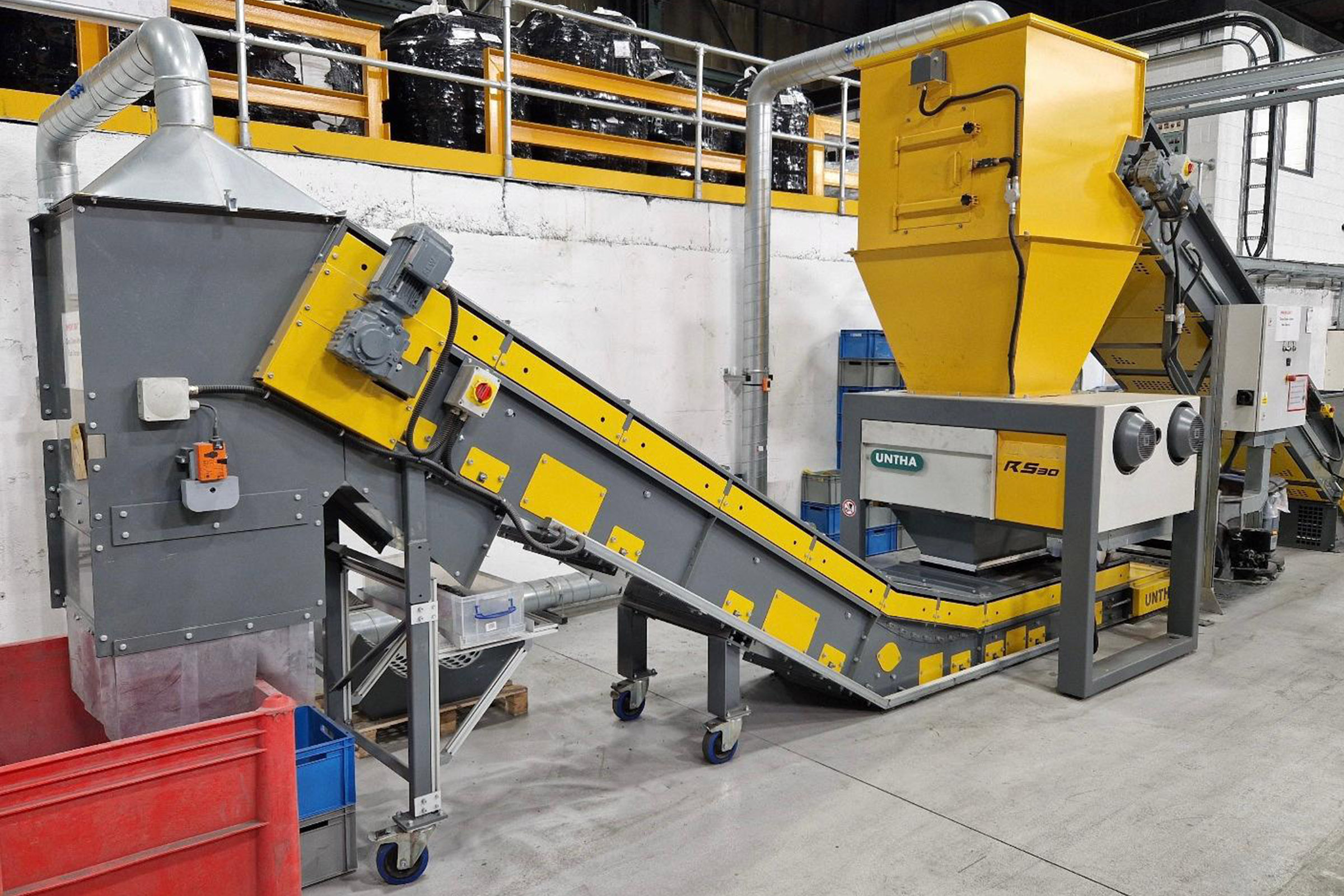
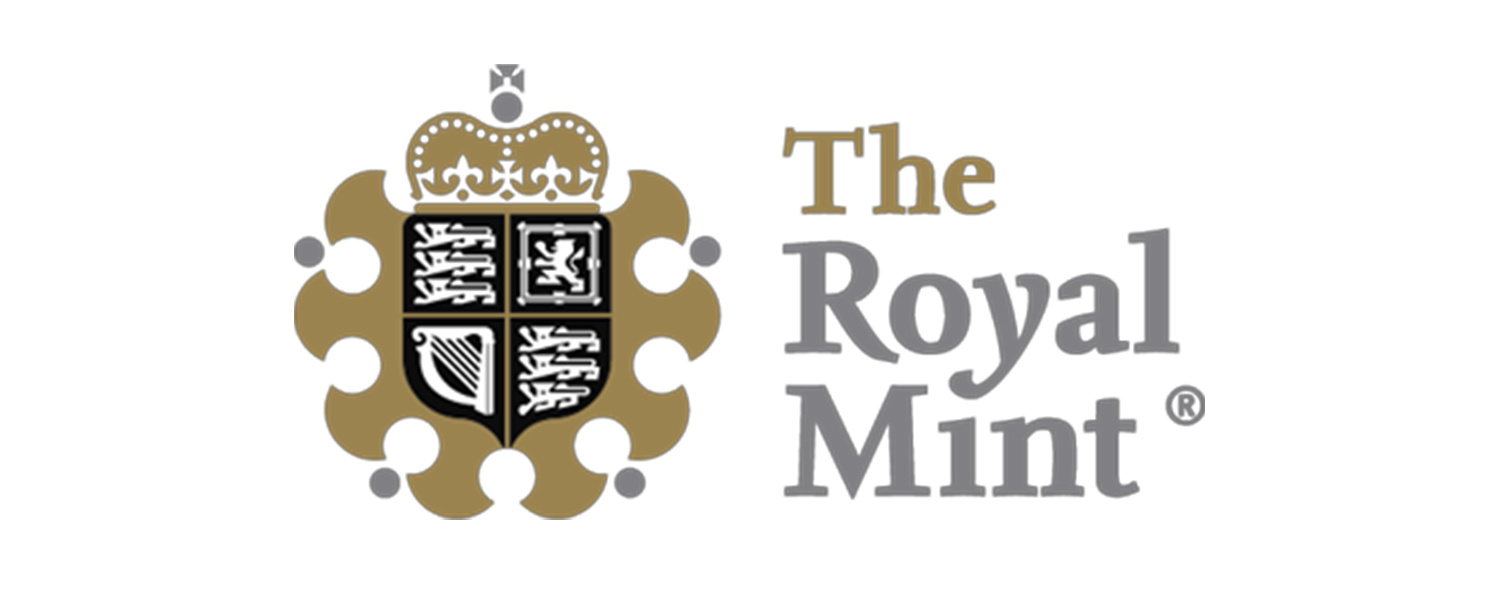
As the official maker of UK coins, The Royal Mint boasts a 1,100-year heritage in coin manufacturing and engineering. It’s also believed to be one of our nation’s oldest businesses. Owned by His Majesty’s Treasury, the company produces coins, medals, and precious metal products, alongside offering investment opportunities in gold and silver. Now, driven by a keen commitment to sustainability and changing economic conditions, The Royal Mint is pioneering an industry-first facility dedicated to recovering precious metals from e-waste.
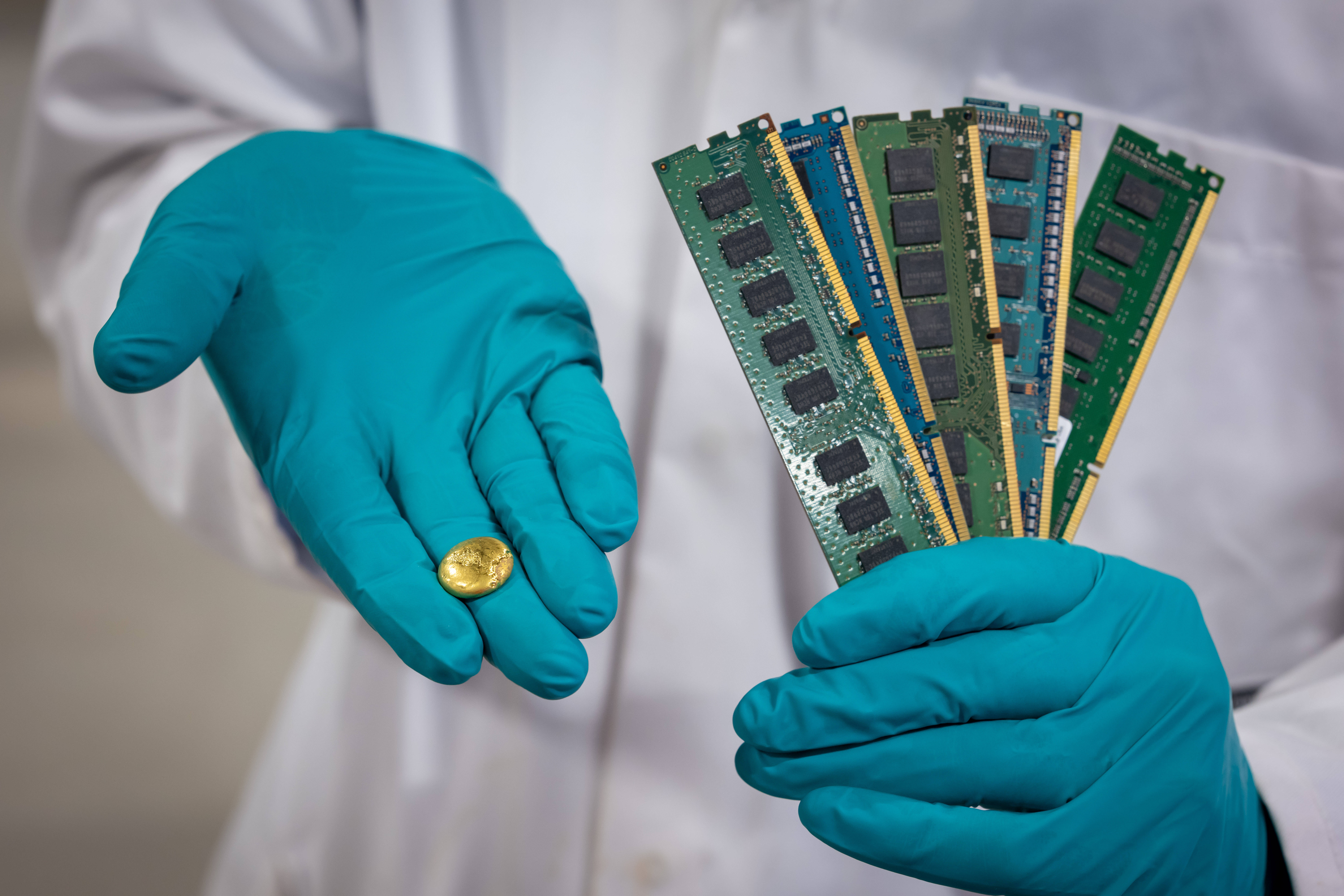
As one of the world’s fastest-growing waste streams, expected to reach 82 million tonnes by 2030, e-waste poses a significant challenge. But The Royal Mint’s multi-million-pound, 35-acre site in South Wales is at the cutting edge of maximising the untapped resource value of WEEE, with a groundbreaking processing line that extracts gold and other precious metals from printed circuit boards found in discarded electronics.. The recovered gold is transformed into jewellery for The Royal Mint’s luxury jewellery collection, 886 by The Royal Mint. They are developing a closed-loop approach that reduces its carbon footprint and minimises reliance on mined materials.
REQUIREMENTS
Efficient and precise shredding of printed circuit boards for material recovery
Robust machinery capable of handling 4,000 tonnes of printed circuit boards from e-waste each year
Seamless integration into a complex and dynamic processing line
Long-term reliability, performance, and maintenance support to maximise ROI
Shared ambitions to push the boundaries of sustainable precious metal processing
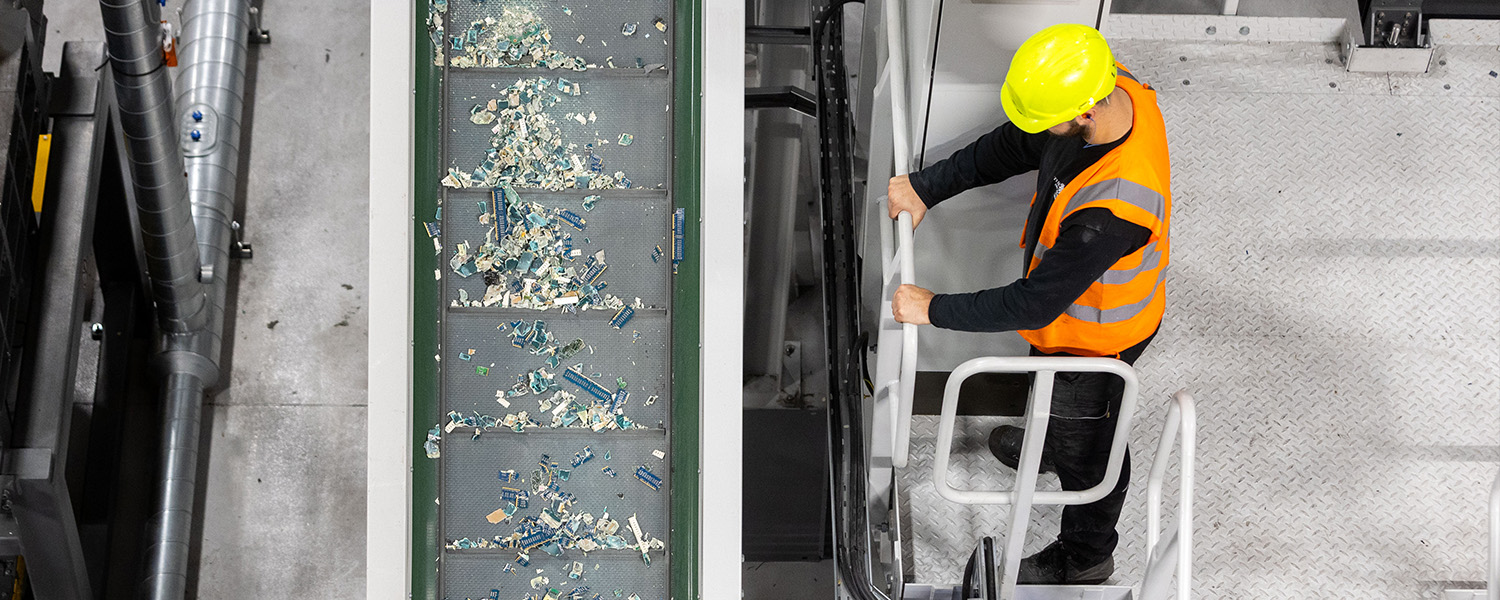
The Royal Mint’s e-waste recovery facility is an industry first, liberating precious metals from discarded electronics. The process begins when circuit boards are tipped into a hopper, and a sophisticated system of technologies including conveyor belts, vats, ovens, and three UNTHA RS30 shredders, takes over. The UNTHA machines break down the circuit boards into precise granulate particles, ensuring metals and non-metals are effectively separated for further treatment.
The material then undergoes a series of complex steps to maximise recovery. Base metals are extracted and sold to refiners, while gold-laden fragments are treated with a first-of-its-kind chemical produced by The Royal Mint’s clean tech partner, Excir. In just minutes, the solution selectively leaches out more than 99% of the gold to produce a fine powder, which is filtered and dried before being heated in a furnace to form pure gold nuggets for remanufacturing.
And with up to 70% of its energy sourced from on-site solar, wind, and heat power, The Royal Mint’s green promise is evidenced even further. The company is also exploring whether non-metal components can be repurposed into building materials.
Our installation team was among the first to take residency onsite. Seeing the UNTHA van parked in what is now a groundbreaking precious metals recovery hall, with a complex processing line that has stopped the entire WEEE industry in its tracks, demonstrates how important our role has been in aiding The Royal Mint’s bold ambitions.
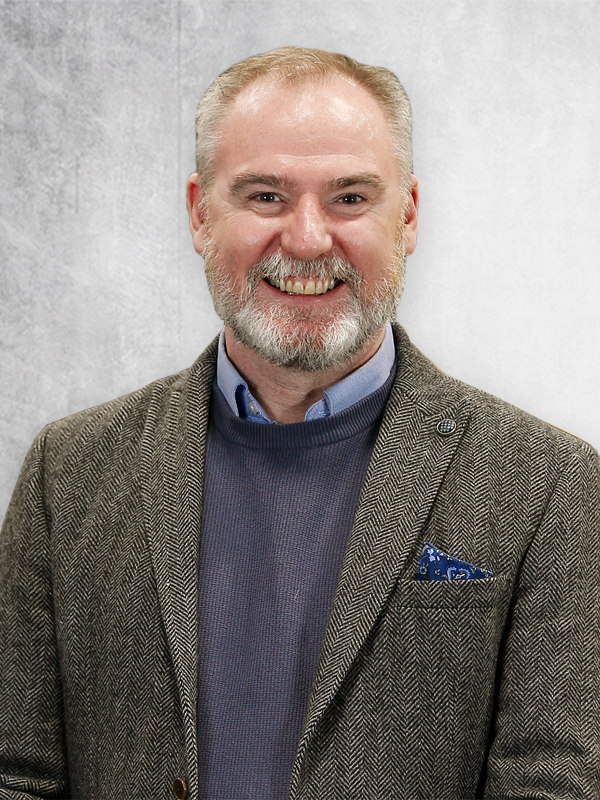
Marcus Brew
Managing director, UNTHA UK