Products
Single-shaft shredder for efficient coarse, medium and fine shredding of different material flows
High throughput and maximum availability
Very low operating costs thanks to UNTHA Eco Power Drive
Sturdy machine design
Easy to maintain and service
The efficient UNTHA Eco Power Drive is a true master of economy, consuming up to 75% less energy than diesel-powered shredders.
The efficient UNTHA Eco Power Drive is a true master of economy, consuming up to 75% less energy than diesel-powered shredders.
The static shredder can easily be controlled via an ergonomic operating terminal with a 7” colour touch display.
The robust construction of the XR machines facilitates low-vibration running in tough working conditions. In this way, difficult materials can also be shredded without any problems.
The XR shredder represents outstanding efficiency, flexibility and reliability when shredding different material streams.
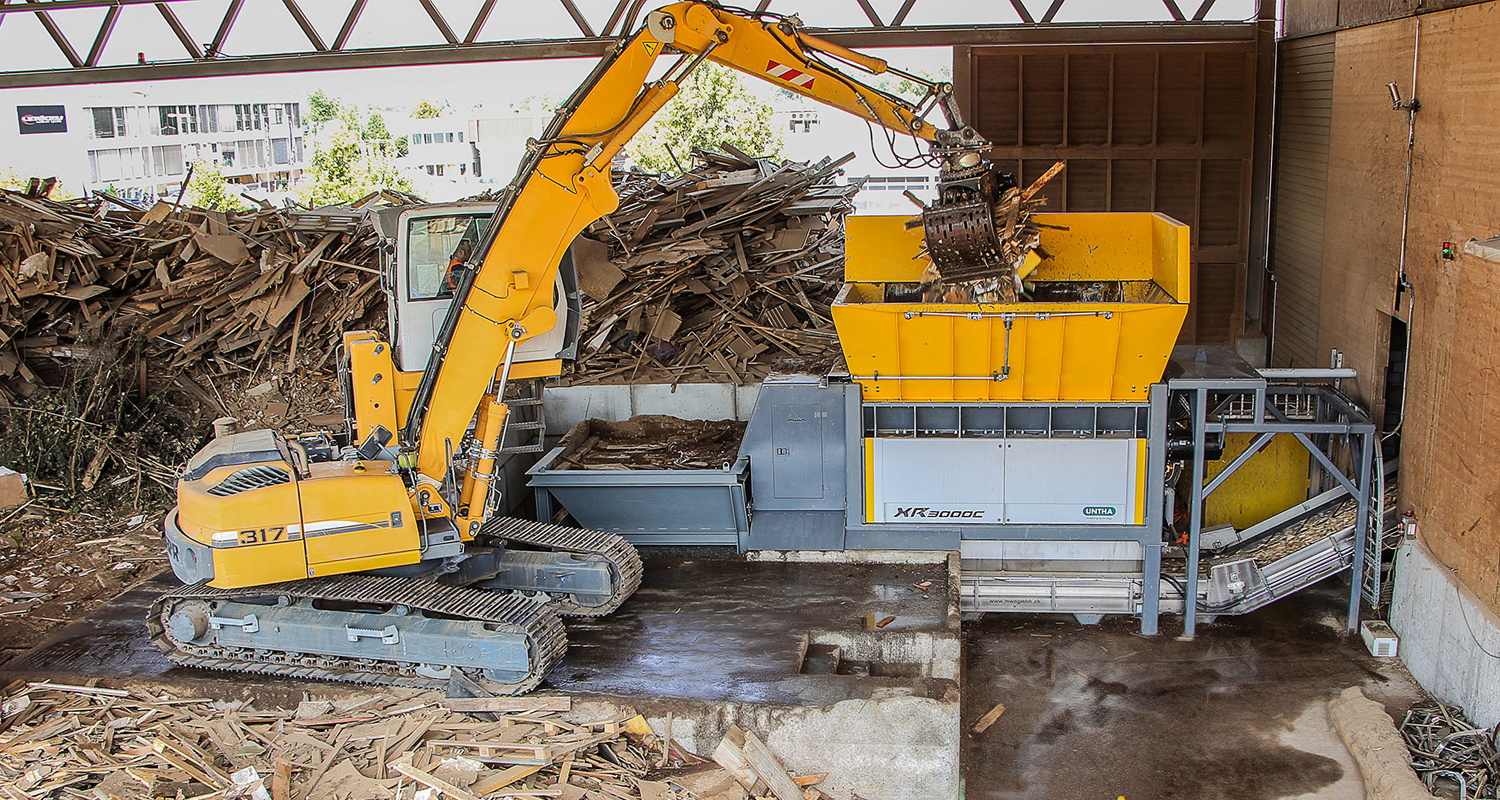
Our low-speed single shaft shredder can cope with even the most difficult of materials. It doesn’t matter whether industrial, commercial or domestic waste, bulky waste, waste wood, metal, pulper ropes or plastic bales. The XR class shredders provide to an equal extent a strong pre-shredder for the recycling of bulky materials, or for the single-stage processing of alternative fuels. Due to the large range of different perforated screens and cutting tools, an XR shredder can be adapted precisely to your technical requirements.
Depending on the material and fraction sizing, different cutting systems featuring different blade shapes are available for the RC, C and XC systems. This makes homogeneous particle sizes from 25 mm to 300 mm possible. Large quantities are no problem for the XR: The throughput lies between 10 t/h and 70 t/h, depending on the material properties and the perforated screen diameter. The system blades can easily be accessed via the service flaps, and can easily be undone via their screw connection.
The slow rotor speed means that the machine is particularly resistant to foreign objects, meaning that it is protected against damage.
Foreign objects can be easily and quickly removed from the shredder via the foreign object flap. An optional hard facing layer also substantially increases the lifetime of the rotors in
case abrasive materials are shredded.
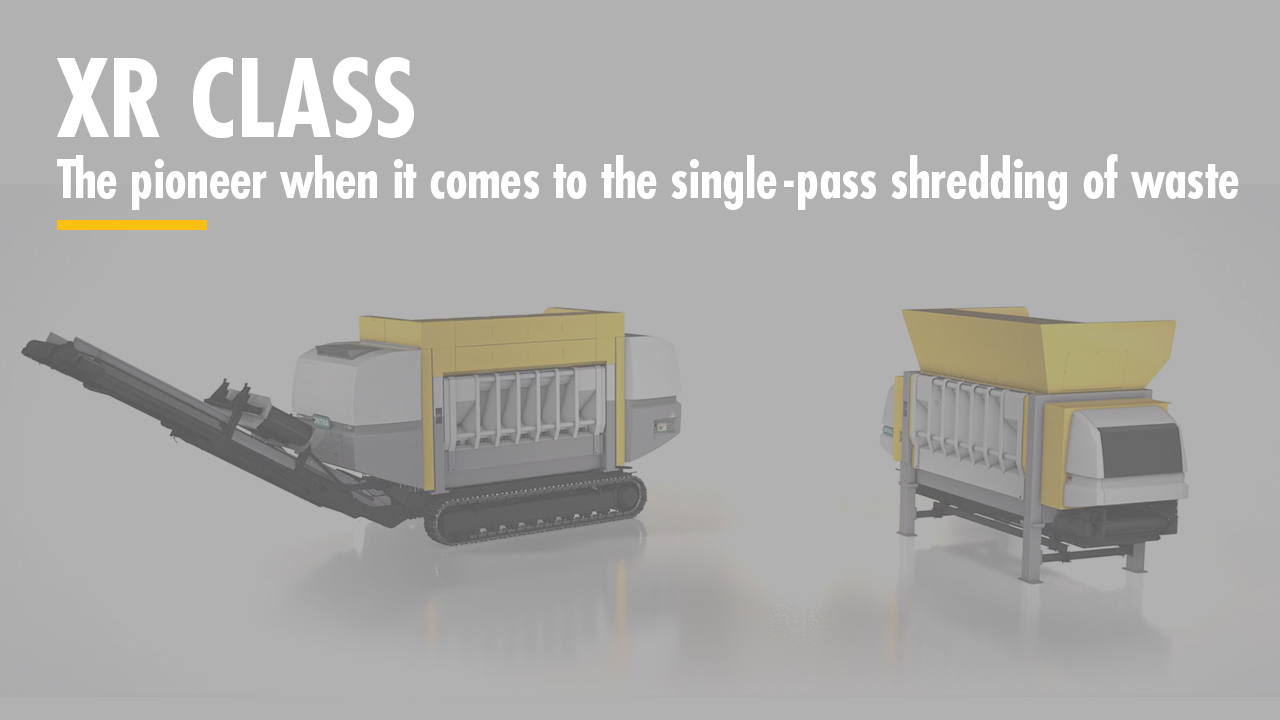
The static XR machine is particularly efficient and economic due to single stage processing. Minimum operating costs with maximum performance are the particular advantages of this shredder type. Using the energy-saving UNTHA Eco Power Drive with water-cooled synchronous motor, you can save up to 75 % energy costs with a higher efficiency in comparison to conventional diesel-hydraulic shredders. The wear-free direct drive on our shredder also reduces maintenance costs, as no belts or shaft stubs are required. The load-dependent speed control ensures a high machine shredding throughput.
The special, solid steel frame design, high quality and rugged construction permit use of this low-vibration industrial shredder in difficult working conditions. Due to its compact design, the machine can easily be integrated into existing plant concepts. Manageable investment costs and low operating and maintenance costs make this solution particularly attractive. Our project managers are happy to assist you in planning your individual and reliable shredder.
These materials can be shredded with the XR2000/3000:
Depending on the material and fraction size, several cutting systems with different blade shapes are available with the RC, C and XC system. The cutting systems allow fraction sizes from 25 to 300 mm.
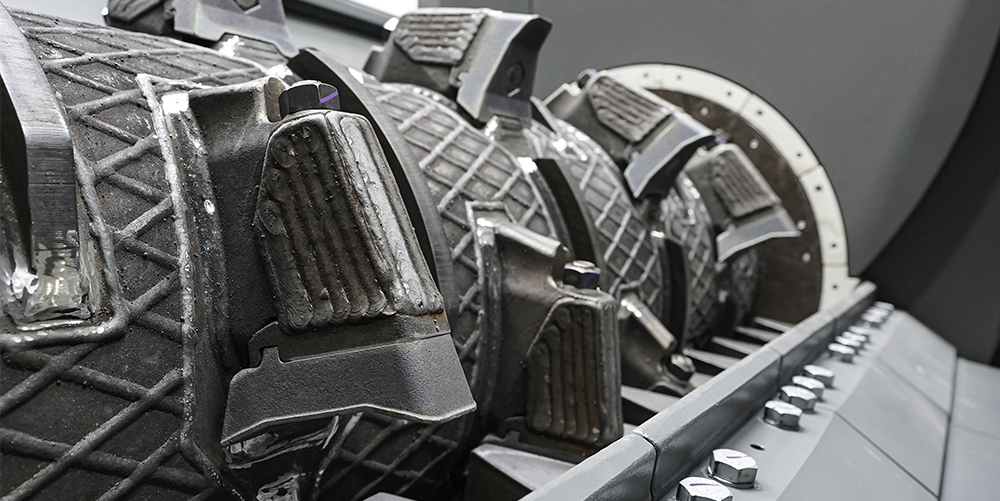
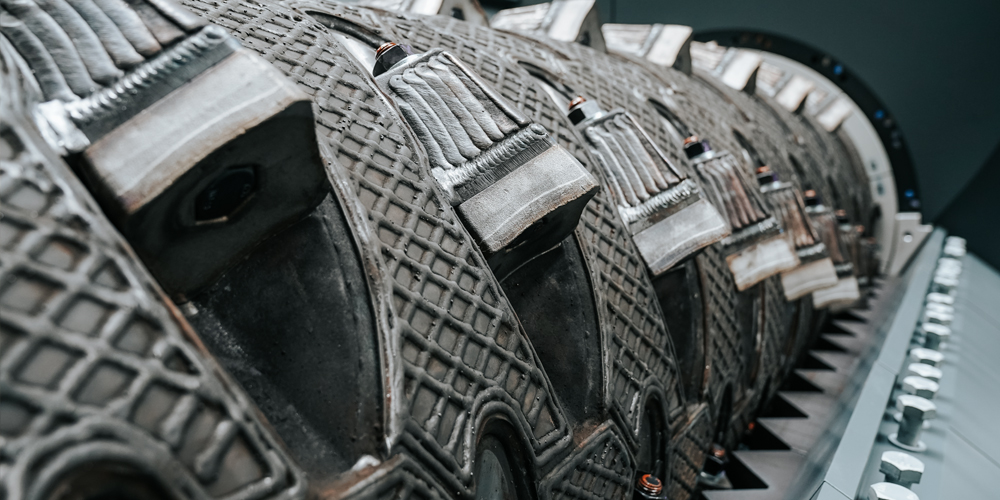
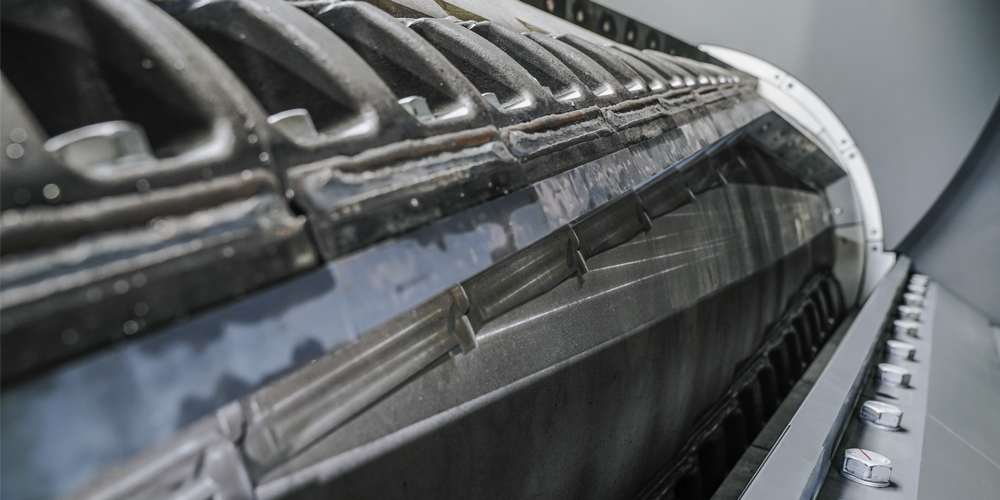
The RC cutting system was specifically developed for the coarse pre-shredding of different material flows and for high throughput rates of up to 70 t/h. The purpose-built shape of the blades ensures a particularly aggressive intake behaviour for the material. The cutters and the stator bar may be welded on again at the end of the service life.
Obtainable fraction sizes: 100 - 300 mm
Thousands of customers from diverse industries around the world already place their trust in the reliable UNTHA name.
The shredder is so flexible that we are able to process not just grade 1 to 3 waste wood, but also grade 4 waste wood. The metal we remove from the wood is sold on to the steel industry.
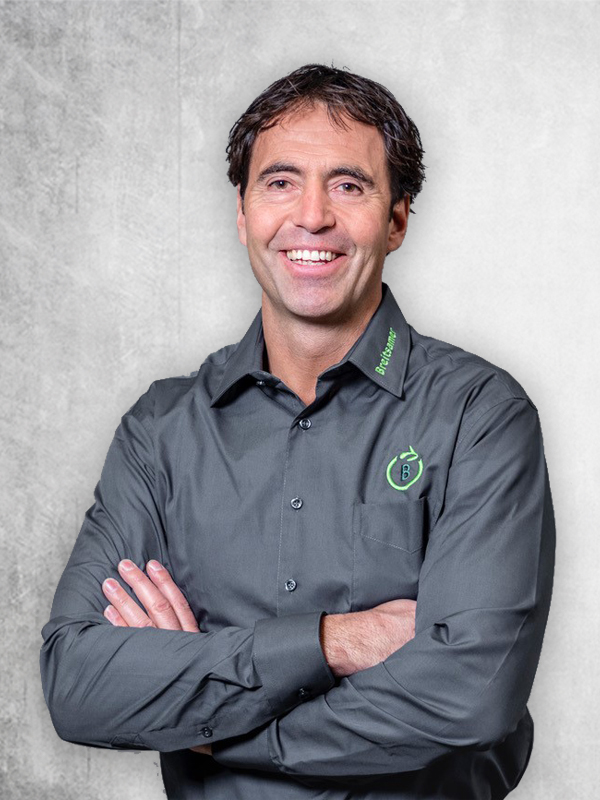
Thomas Breitsamer
Managing Director
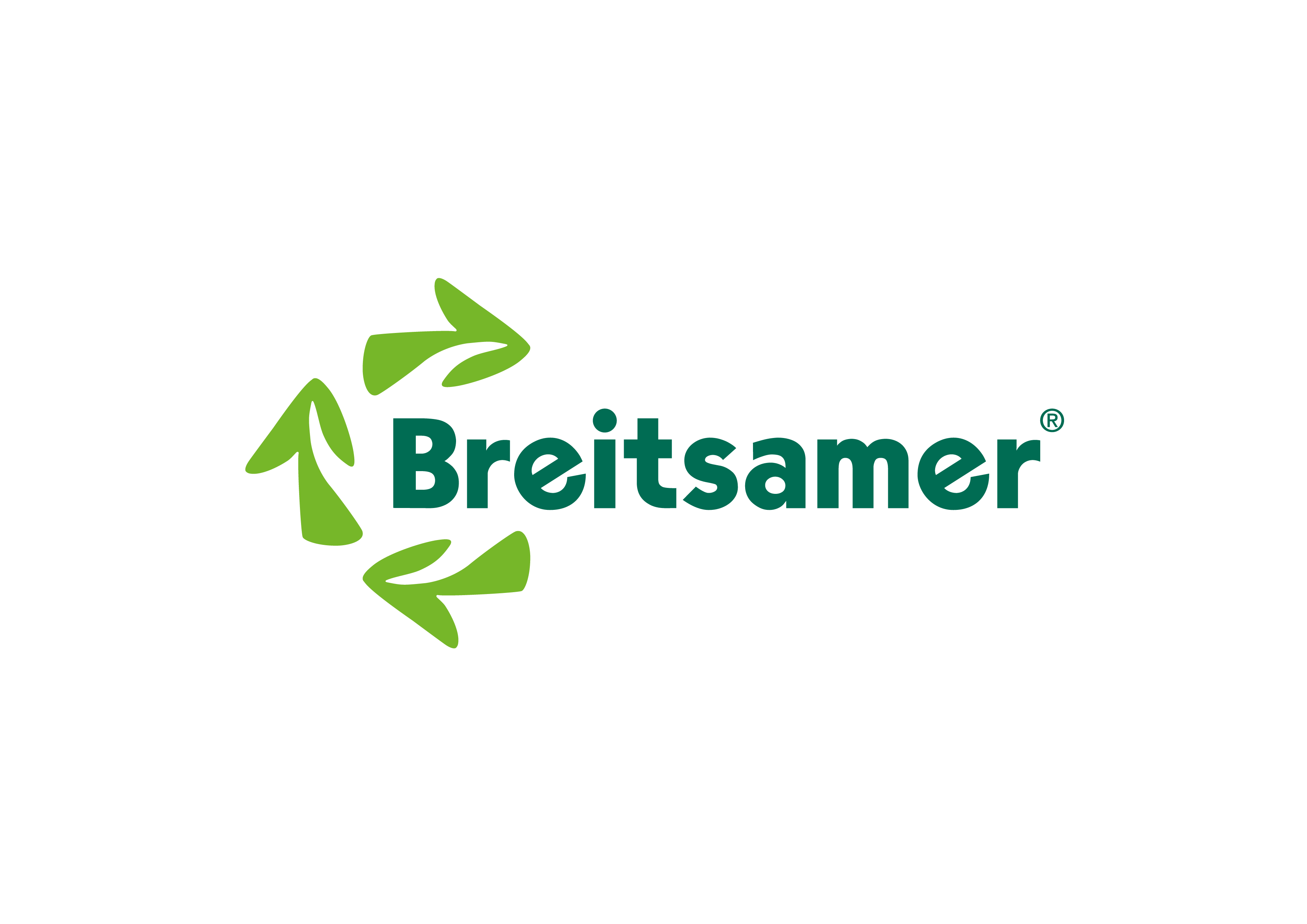
For special requirements, we offer custom-made accessories for this shredder.
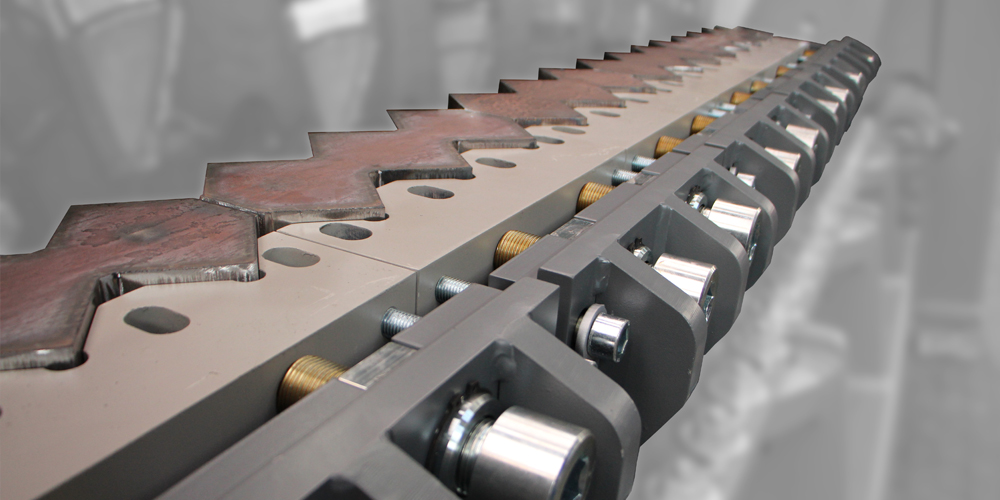
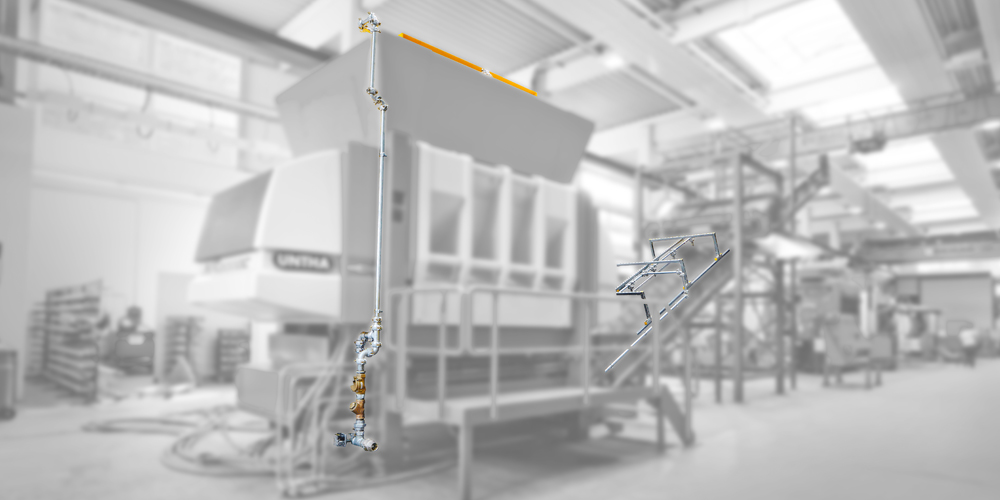
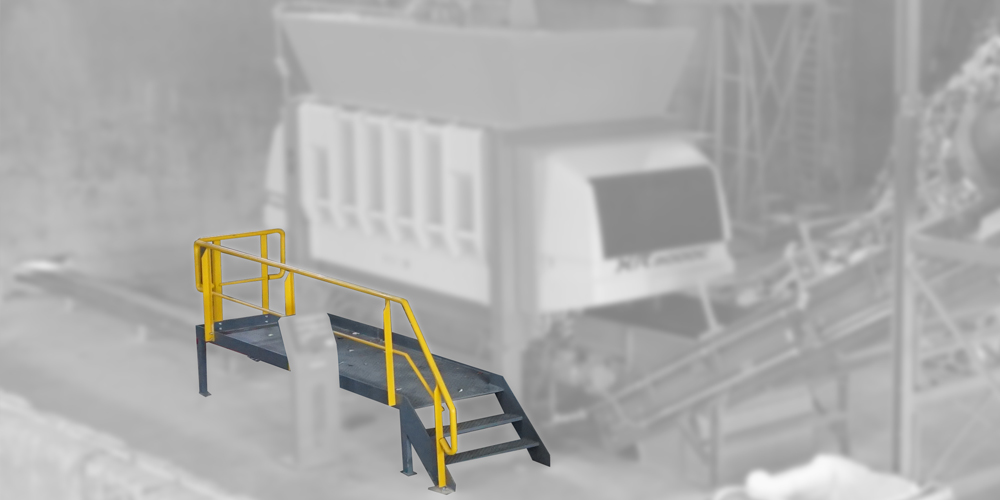
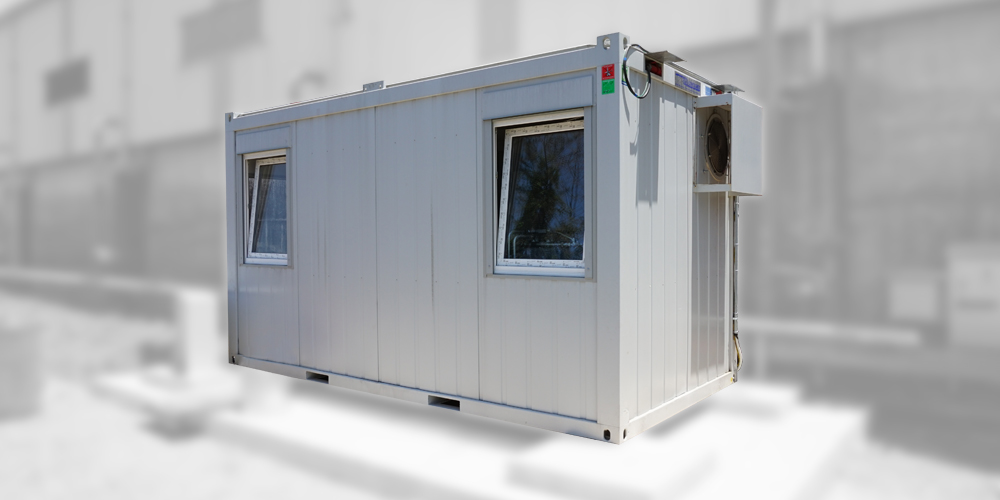
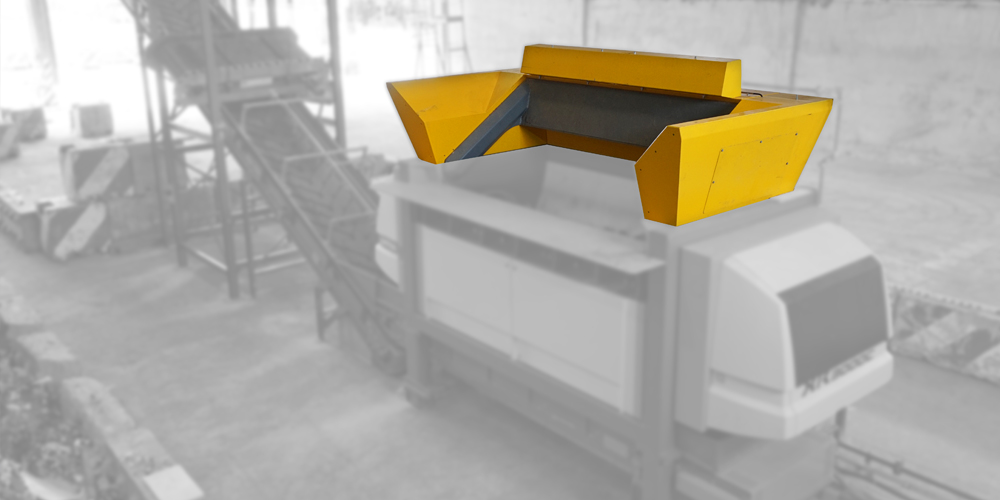
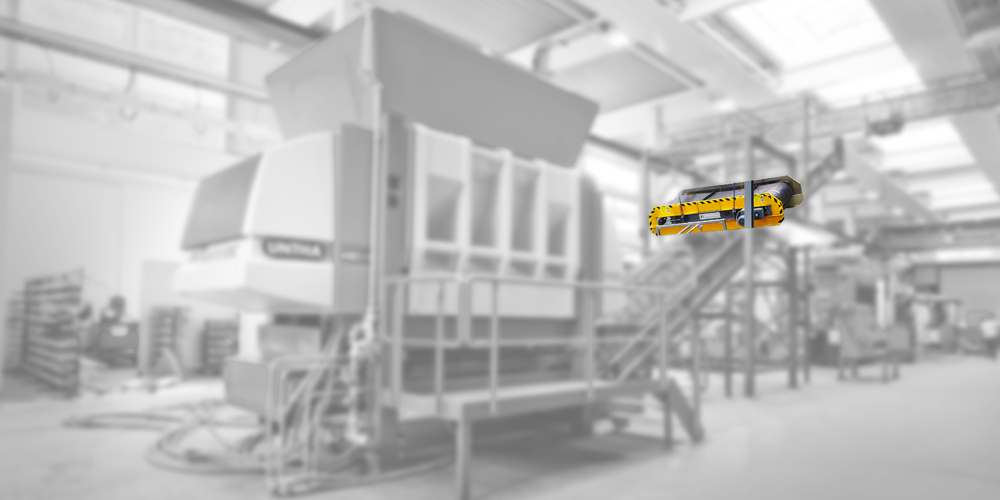
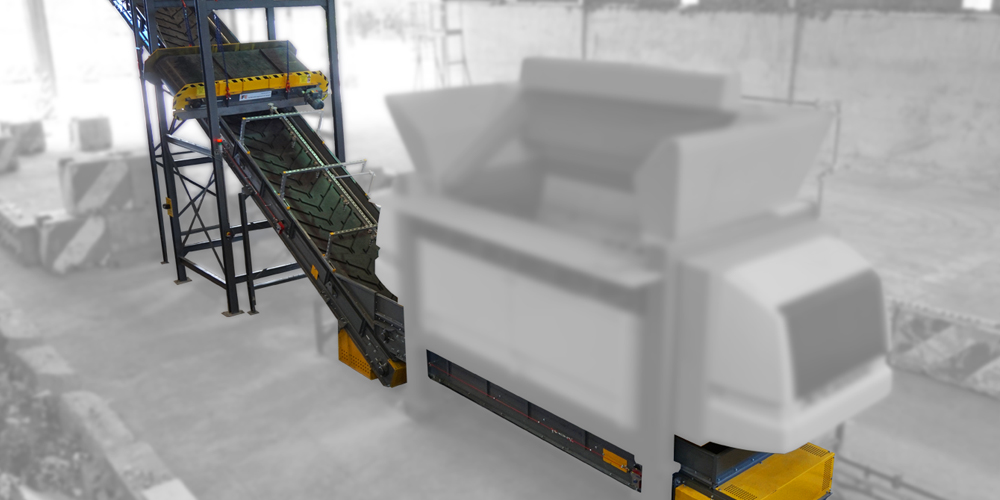
The adjustable main cutting bar offers you the option to adjust the cutting opening. The shredder can be optimally adjusted for the material to be shredded and the required discharge fraction.
This option is only available for the C cutting system.