Keitel Haus from Brettheim/Baden-Württemberg in Germany produces prefab houses made from timber panels. The production process yields waste wood in a wide range of sizes, primarily solid wood and cuts from panel materials. Two UNTHA wood shredders are in continuous operation for the shredding of the waste wood and the production of high-grade wood chips for thermal recovery.
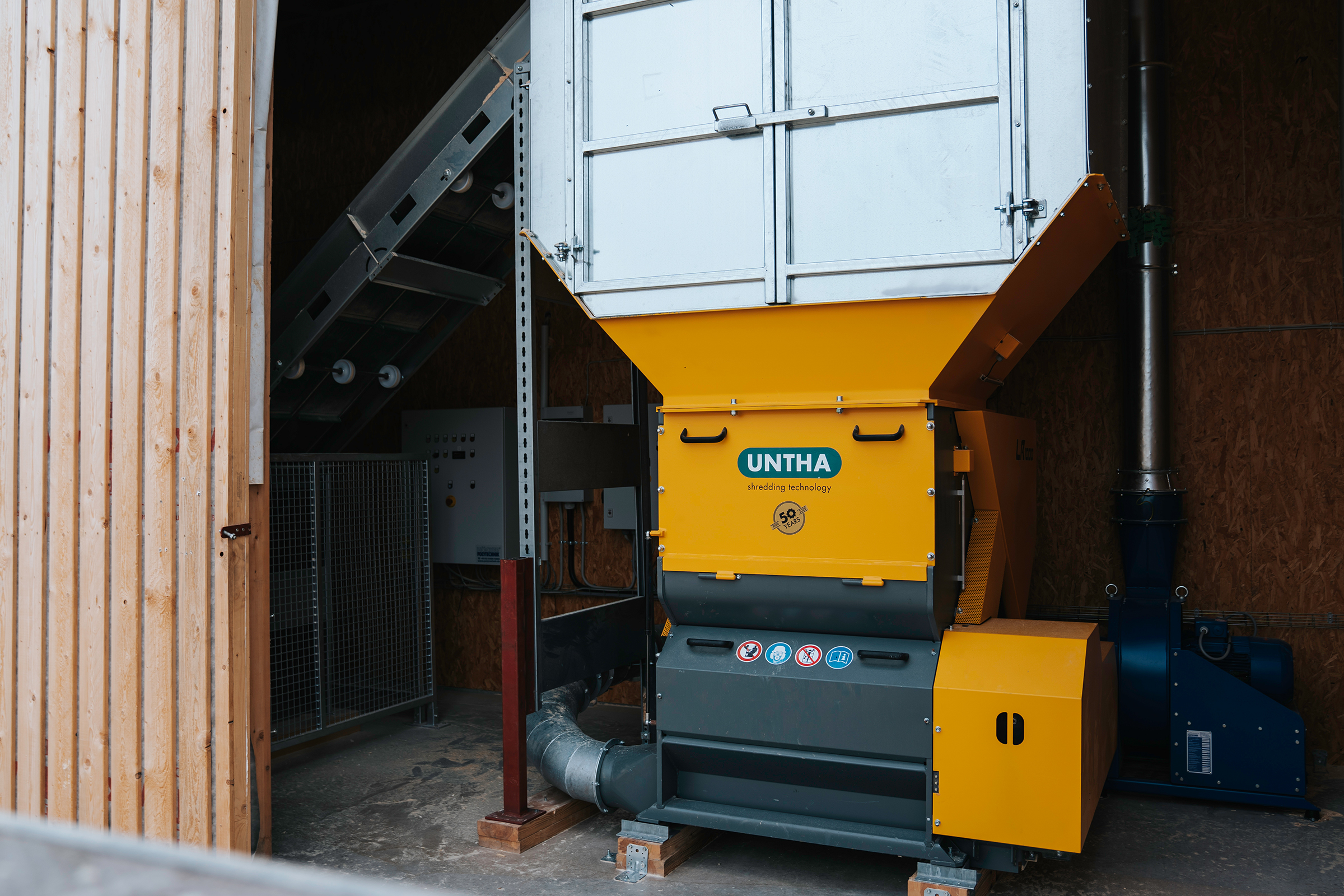
Keitel Haus, a family business that goes back to 1929. Since the 1970s, the site in Brettheim has been producing around 200 prefab houses made from timber panels per year. The company has 160 employees and its strength lies in individualised design. Keitel Haus has won numerous awards, for instance the Hausbau Design Award and the Deutsche Musterhauspreis.
LR1000 for waste wood shredding
Since 1999, the company has been using an UNTHA wood shredder to process its waste wood. Following the decision to expand the business, Keitel Haus had decided to purchase another shredder in 2020. As the first UNTHA had been running for many years to the full satisfaction of Keitel Haus, the company opted for a second UNTHA shredding solution, this time the LR1000. “The biggest factor for us was that over all those years we never had any issues with the first unit”, explains Technical Director Heiko Kreiselmeyer. “UNTHA offers a highly reliable service. If we have any questions, we immediately get competent feedback.” With the LR class, UNTHA offers a family of machines that guarantees compact shredding for carpentry shops, joineries, sawmills, and other timber-processing businesses of any size. Overall, the LR series stands out for its efficient cutting system, long lifespan and outstanding
reliability. All models are efficient, economical and maintenance-friendly, ensuring a homogeneous output material for users, combined with low cost and with little effort in terms of operation.
Perfect combination of shredding and conveying technology
At Keitel Haus, all the waste from the production process, both laminated timber and solid construction timber, is put through the two UNTHA shredders. Keitel Haus thus produces almost 2,500 m3 of material for thermal processing every year. The waste wood is taken directly to the shredder via several conveyor belts, and the wood chips are transported to the storage silo by means of a suction system. From the silo, another conveyor system takes them to the heating facility, located just below the silo.
Shredding as the most important element of heating technology
As a rule, the wood chips suffice to operate not just the entire heating system of the Brettheim site, but also a neighbouring building, an abattoir. Anything that Keitel Haus can’t use for heat production on site is loaded onto trucks using conveyor technology and taken to businesses in the area that also use wood chips. “Overall, the combination of UNTHA shredder, customised conveyor technology and in-house heating plant makes for an environmentally friendly, economic way to process and utilise the company’s waste wood. The efficient shredding of the waste wood is crucial for the smooth running of the heating plant, and we believe that UNTHA shredding technology is handling this aspect economically and sustainably. At Keitel Haus, we are happy to recommend UNTHA shredding technology without reservation,” says Heiko Kreiselmeyer.