Holzbau Gerstenmayer invests in UNTHA shredding system for residual wood
Holzbau Gerstenmayer is a timber construction company based in Karlstetten in Lower Austria. Business has grown steadily in recent years, as have the company’s residual wood volumes. For this reason, the company has invested in an LR1000 shredder by UNTHA shredding technology.
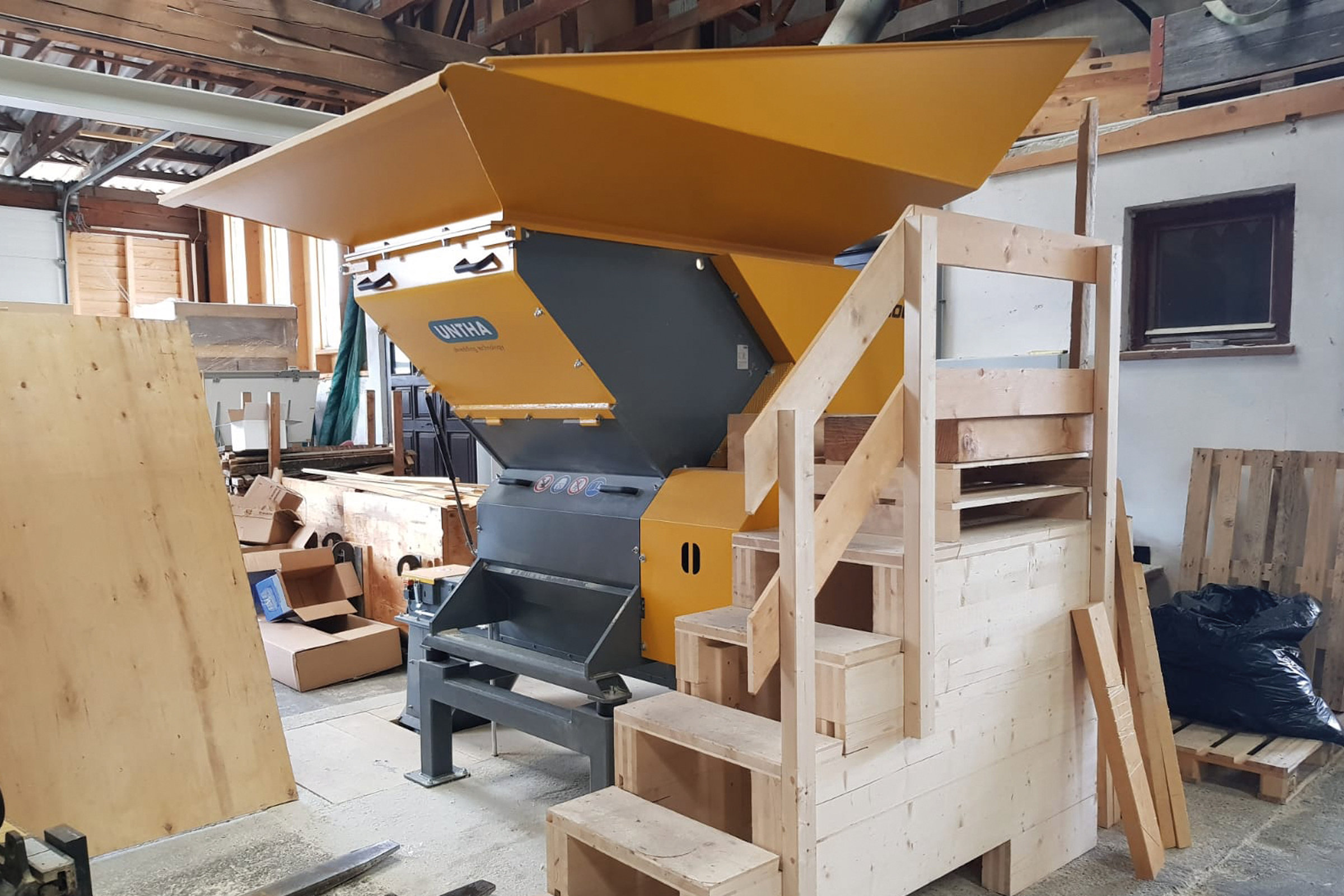
The company was founded as a sawmill and carpentry shop in 1903 by the great-grandfather of its current proprietor, Peter Gerstenmayer, and has been a family business for four generations. It specialises in complete solutions for timber frame and solid wood constructions; from the first design, all the way to the building application and the contractor’s plans, the energy performance certificate and acceptance by the customer. Ten highly skilled employees use two fully automated, CNC-controlled joinery systems to produce roof frame and hall structures, as well as special constructions for individual projects and contract joinery constructions.
Trusting in UNTHA quality
Over the years, residual wood volumes have grown steadily. At the same time, legal requirements with regard to suction, filter and silo technology have become more stringent. Gerstenmayer thus decided to rethink its entire approach towards residual wood processing, making it fit for the future. Having used the robust LR700 from UNTHA for the reliable shredding of residual wood with minimal maintenance and energy requirements for almost 20 years, it seemed obvious to once again use the tried-and-tested technology provided by the premium manufacturer from Kuchl. Following a period of intense consultation, a complete system including conveyor technology, was developed jointly with the customer, based on the LR1000 with its 45° machine frame that would make it possible to process large timber profiles. Thanks to the oversized machine frame, larger volumes of residual wood volumes may be processed and shredded within a very short period and in a single sitting.
LR1000: energy-efficient and wear-resistant
The customer had specified a throughput of around 800 kg/h. Thanks to the aggressive LR cutting system, the standard rated capacity of 22 kW with just 27 cutting blades was sufficient to fulfil these ambitious demands. When it comes to operation and maintenance friendliness, the LR1000 is also hard to beat: To utilise the maximum lifespan of the cutting blades, they need to be turned around just once. The valve technology is designed in such a way that guides are not required, eliminating both wear and maintenance in this area. A hopper structure increases the filling volume of the machine and makes it possible to also use large crates and shovels for feeding the machine, in addition to manual and forklift-based loading. Cabinet heating and low-temperature lubricants mean that the machine runs safely over decades, even at temperatures way below zero. Managing Director Peter Gerstenmayer is convinced that the investment will pay off: “The overall concept provided by UNTHA during the project planning phase and the high level of reliability and cost-effectiveness of the UNTHA machines we have been using for the last 20 years have once again made us opt in favour of UNTHA. And by the way, the LR700 was not taken out of service, but sold on to a partner business where it is still performing well!”
UNTHA provides complete solutions
Another point in favour of UNTHA shredding solutions is that the company offers its customers a one-stop-service, from planning to commissioning, including all the peripheral equipment. Gerstenmayer has also leveraged this advantage when it comes to conveyor technology, where UNTHA is able to fall back on its long-standing cooperation with an Austrian manufacturer of conveyor technology. The brief specified that the granulate had to be dropped from a height of approximately seven metres, using a long discharging screw, before being spread evenly by a spreading auger. The screw and the auger had to be controlled via the shredder’s control system, requiring lead-in and lead-out times, the safety- technological integration of the bunker doors and also the shutdown of the unit in case the bunker reached maximum capacity.