The world of metal recycling is never straightforward, with sometimes the slightest market variable causing significant volatility in global trade.
That’s why, when the economy slows, scrap firms need to be as cost efficient as possible – think maximum yield, optimum recycling quality and low maintenance recycling equipment. And when markets are busy, operators need the confidence they can ramp up their facilities with ease, handling more throughputs and varied material streams, without worrying about the capabilities of their machinery ...
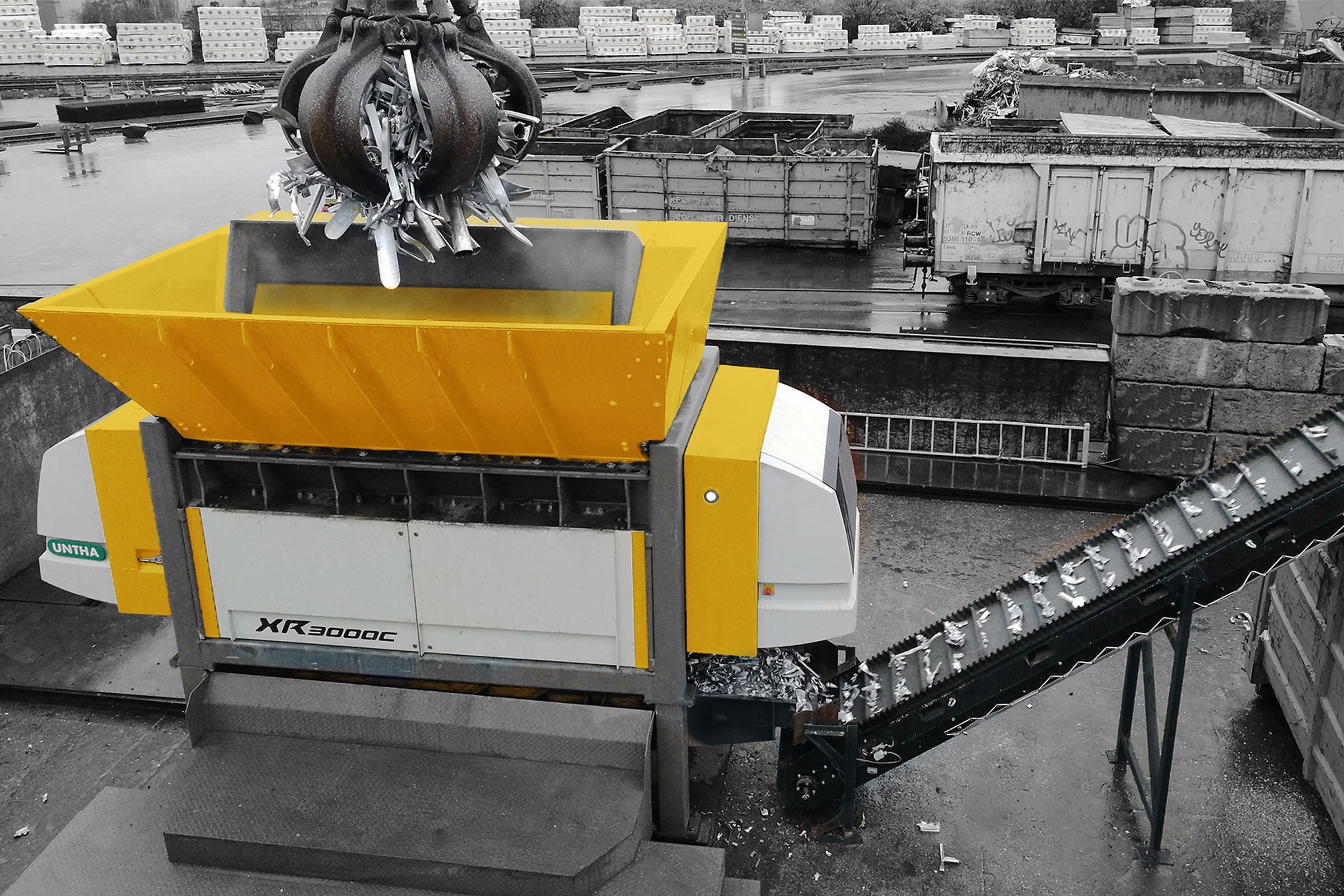
The world of metal recycling is never straightforward, with sometimes the slightest market variable causing significant volatility in global trade.
That’s why, when the economy slows, scrap firms need to be as cost efficient as possible – think maximum yield, optimum recycling quality and low maintenance recycling equipment. And when markets are busy, operators need the confidence they can ramp up their facilities with ease, handling more throughputs and varied material streams, without worrying about the capabilities of their machinery.
That’s why we – at UNTHA – have continued to invest in our range of metal shredders. They’re more hard-wearing than ever before, their uptime statistics are impressive and their ability to handle ‘unshreddables’ mean the equipment is protected from damage that could
otherwise be caused by foreign objects.
And we’ve also continued to work with MRFs, metal recyclers and scrap merchants, to help them achieve more from their plants…
Effective material liberation strategies
Many operators rely only on traditional, cumbersome shear equipment to cut metals down, because the perceived high-wear nature of metal shredding is deemed too cost prohibitive.
However, dependence on this basic shear methodology means alternative sorting, grading, separation and size-reduction processes are overlooked, and metal recyclate quality typically remains low as a result.
Machinery such as high-speed hammer mills – which work by smashing material into smaller pieces with repeated impact blows – typically create vast amounts of dust. This dust is useless, costly, and it poses a fire and operator wellbeing risk. This process also struggles to achieve the particle refinement required for downstream separation technologies to effectively do their job.
Mindful of the limited revenue potential associated with these approaches, recyclers elsewhere are investing in more sophisticated processing lines complete with shredder, overband magnet to extract ferrous metals, eddy current separator (ECS) to separate out any non-ferrous metals, and optical sorter to clean anything the ECS hasn’t already refined. And the greater the level of quality metals recovered, the higher the revenue potential. The recovery of high-worth Platinum Group Metals (PGMs) and Rare Earth Metals (REMs) could make for a particularly profitable operation.
Ideally, the shredding technology should be slow-speed, with a high torque drive to increase resistance against unshreddables without jeopardising throughput levels. A reinforced machine frame will also offer greater operational stability, and double collar cutting disks will deliver a stronger cutting force. Such factors are key to long-lasting shredder performance, and therefore ROI.
‘Undiscovered’ metal recycling opportunities
Some operators are already familiar with such ‘best practice’ metal recycling methodology, and are consequently exploring the market to see ‘what’s next?’ They’re right to search for further opportunities, because they do exist in the form of ‘wastes’ that are notoriously tricky to handle. But with engineering advancements and clever process design, heightened recovery rates are certainly achievable.
Millions of bulky end-of-life mattresses are disposed of per year, in the UK alone, for example – with many of them being dumped illegally. But it is possible to size reduce 200 of these per hour with slow-speed, high torque and economical machinery, so that clean flock can be used for alternative fuels and the metal extracted for smelting. This is an important waste stream to get to grips with, considering the ambitious landfill diversion targets for mattresses.
But this is not the only tricky application where metal recycling potential remains untapped. The global waste industry is sitting up and paying more attention to tyre processing, for instance, given growing demand for Tyre Derived Fuel (TDF). However, a valuable by-product of a savvy tyre handling line, is metals, which would otherwise remain trapped in these bulky, toxic products. That’s not all – one of UNTHA’s waste wood shredding clients is generating more than €3,500 of revenue per week from the sale of clean metals extracted directly off the magnet belt.
The difference with these latter applications, is that they are renowned for being difficult and, as such, have long been avoided. But so many people are focusing on processing the ‘good’ –
or easy – material. Only by developing ways to treat dirtier or more complex materials will we be able to establish truly closed loop models that turn more ‘waste’ products into reusable resources.
To discuss your metal, WEEE or e-scrap recycling needs, or if you think your bulky waste contains high value metallic content that you’d like to liberate, contact us.