Products
Single-shaft shredder for efficient coarse, medium and fine shredding of different material flows
Mobile shredding concept
Sturdy design with high resistance to foreign objects
High material quality with high throughput performance
Low maintenance expenditures
Low noise emissions
The efficient UNTHA Eco Power Drive consumes up to 75% less energy than diesel-powered shredders.
Due to so-called quick connection power plugs, it is possible to quickly and safely connect and disconnect the machine.
Thanks to its crawler-type undercarriage, the mobile shredder can easily be moved to any spot via remote control.
The XR machines are particularly rugged in construction and can therefore process difficult materials without any trouble.
The XR3000 mobil-e is a revolutionary machine concept in mobile waste shredding. It capitalises on many benefits of an electromechanical drive without having to forego the advantages of a mobile machine. This gives you maximum efficiency and flexibility.
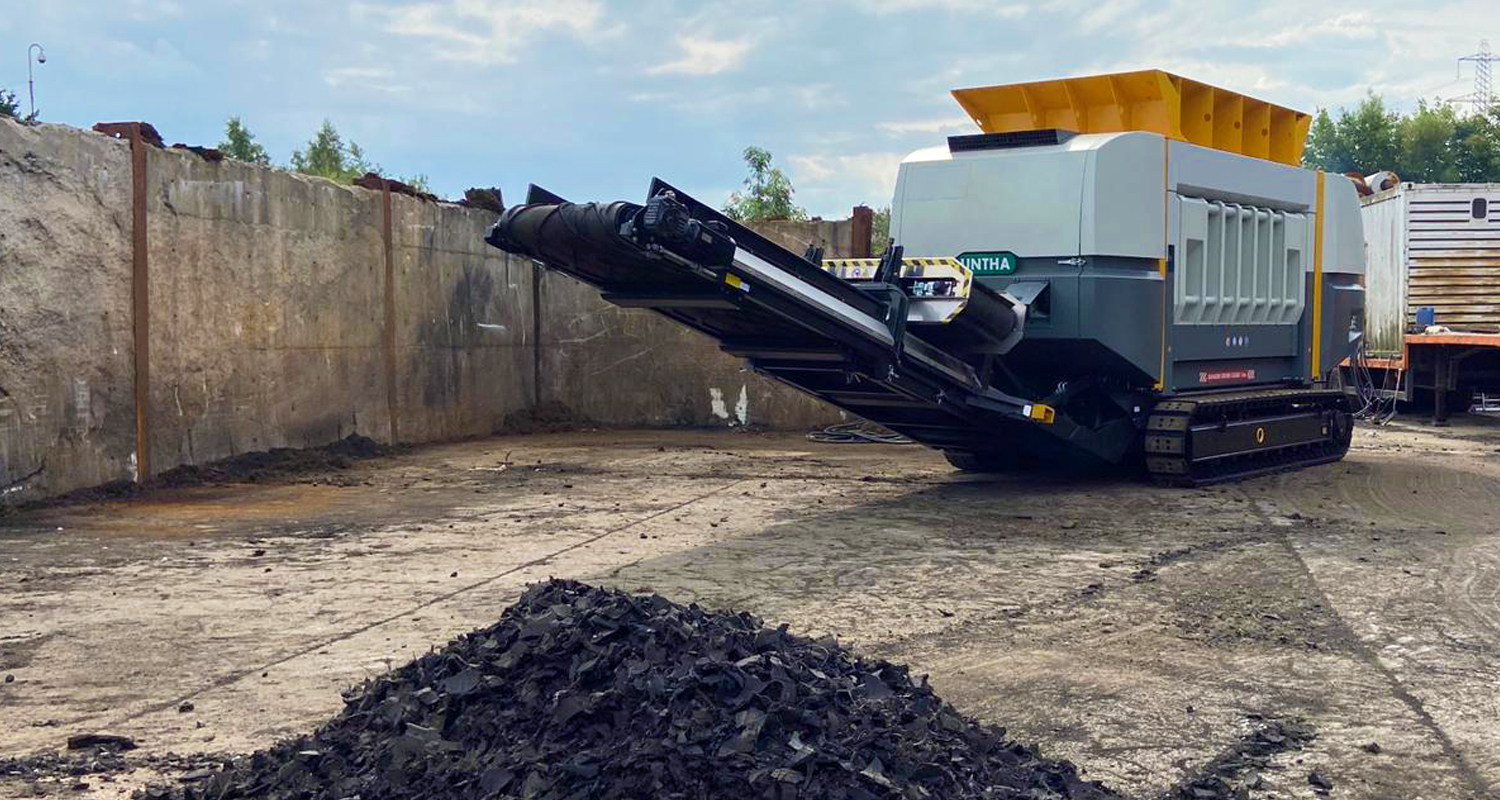
All the advantages of the XR shredder in mobile form: The machine concept of the XR mobil-e shredder is exceptional. For you, this means high efficiency, high profitability and enormous flexibility. Minimal operating costs at maximum performance: The XR mobil-e shredder is a strong workhorse for shredding and recycling your different materials. The single stage processing makes this machine particularly efficient and economic.
Our industrial shredders in the XR class have one particular advantage, which is of course also featured on our mobile shredder: The energy-saving UNTHA Eco Power Drive with water-cooled synchronous motor saves up to 75 % energy costs with increased efficiency in comparison to conventional diesel-hydraulic drive variants. The application possibilities of a shredder in your company are maximised through the mobile variant of the XR machine. For the shredding process, the XR mobil-e shredder is connected with the power supply using a practical quick connection.
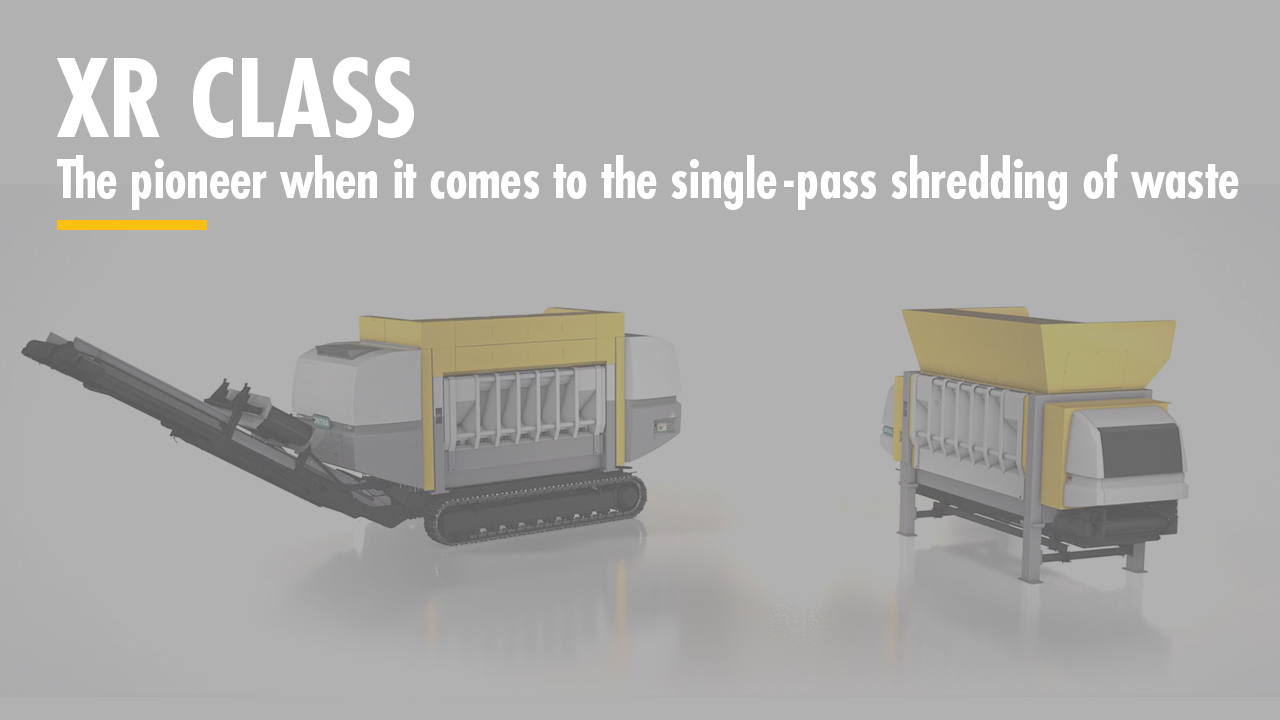
Shredder mobility is ensured through a reliable crawler-type undercarriage in combination with a small petrol-powered engine. The XR mobil-e shredder can be easily moved to any spot via remote control. Due to the large range of different perforated screens and cutting
tools available, the machine can be adapted precisely to your requirements. In this way, for example, homogeneous particle sizes ranging from 25 mm and 300 mm can be achieved. In this way, the XR mobil-e can easily shred bulky, domestic or industrial waste as well as mixed construction or wood waste, and produce a homogeneous alternative fuel for waste incineration plants, cement works, gasification or biomass plants.
In addition, a height-adjustable discharge conveyor belt and an optionally available magnet separator provide you everything you need for the efficient operation of your mobile shredding system. This is a great and comprehensive package from UNTHA for your recycling requirements and for the processing of different materials.
These materials can be shredded with the XR mobil-e:
Depending on the material and fraction size, several cutting systems with different blade shapes are available with the RC, C and XC system. The cutting systems allow fraction sizes from 25 to 300 mm.
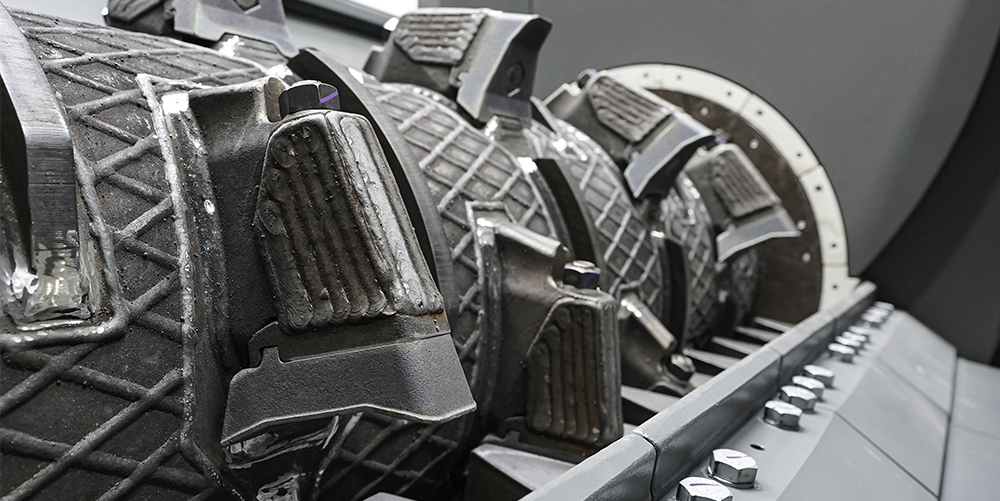
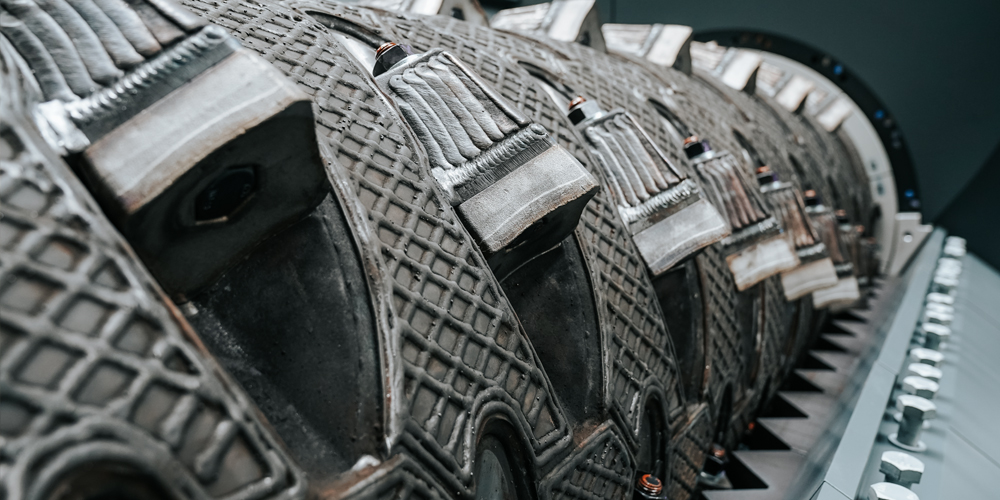
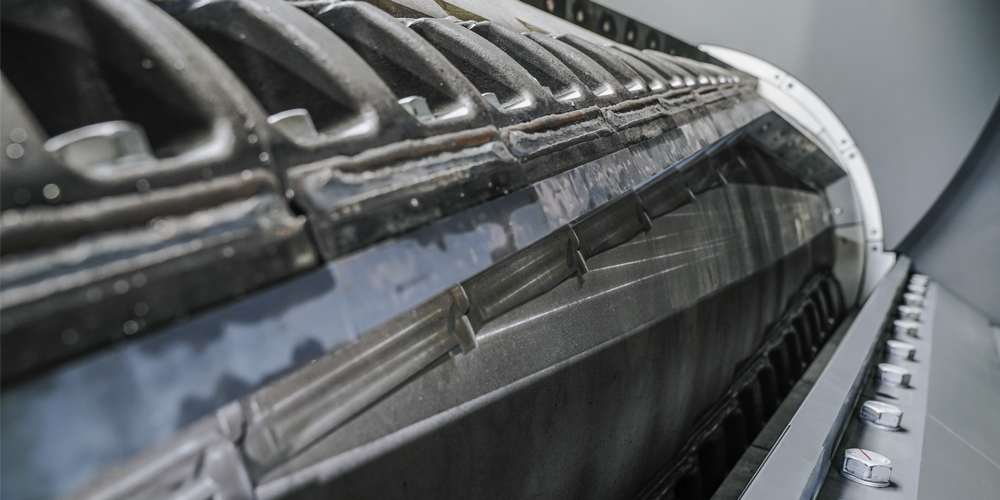
The RC cutting system was specifically developed for the coarse pre-shredding of different material flows and for high throughput rates of up to 70 t/h. The purpose-built shape of the blades ensures a particularly aggressive intake behaviour for the material. The cutters and the stator bar may be welded on again at the end of the service life.
Obtainable fraction sizes: 100 - 300 mm
Thousands of customers from diverse industries around the world already place their trust in the reliable UNTHA name.
The shredder is so flexible that we are able to process not just grade 1 to 3 waste wood, but also grade 4 waste wood. The metal we remove from the wood is sold on to the steel industry.
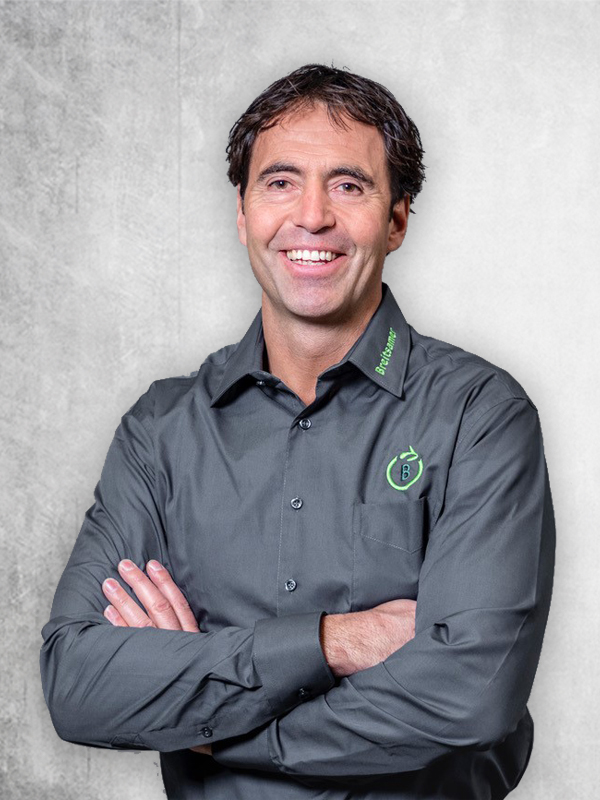
Thomas Breitsamer
Managing Director
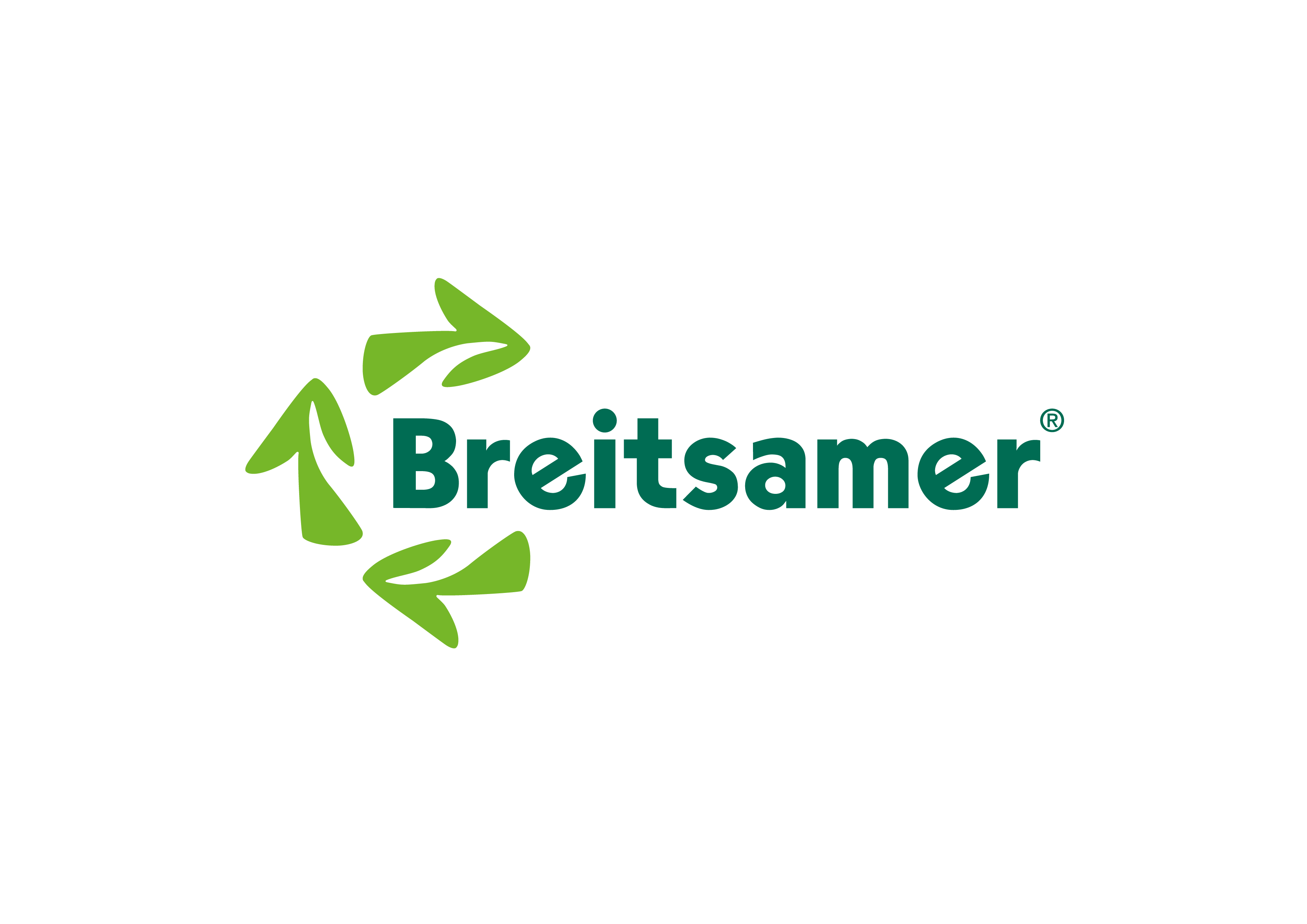
For special requirements, we offer custom-made accessories for this shredder.
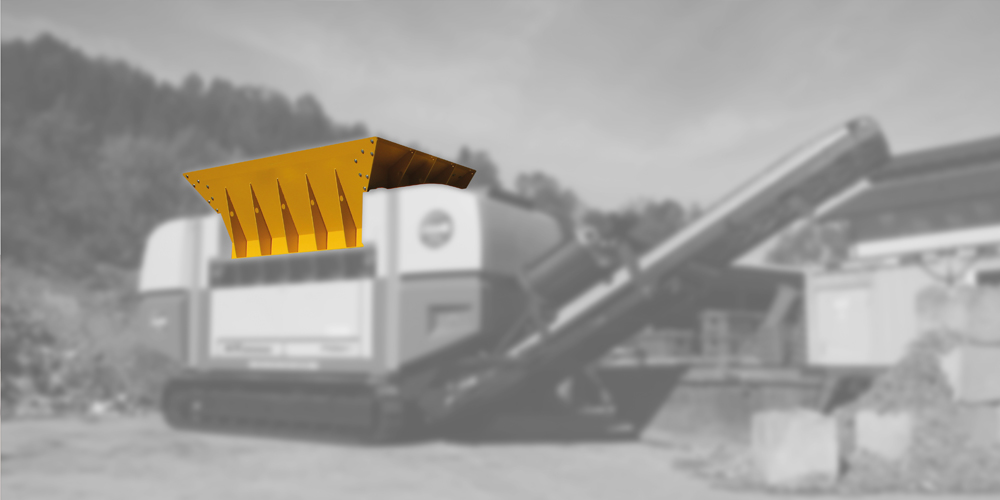
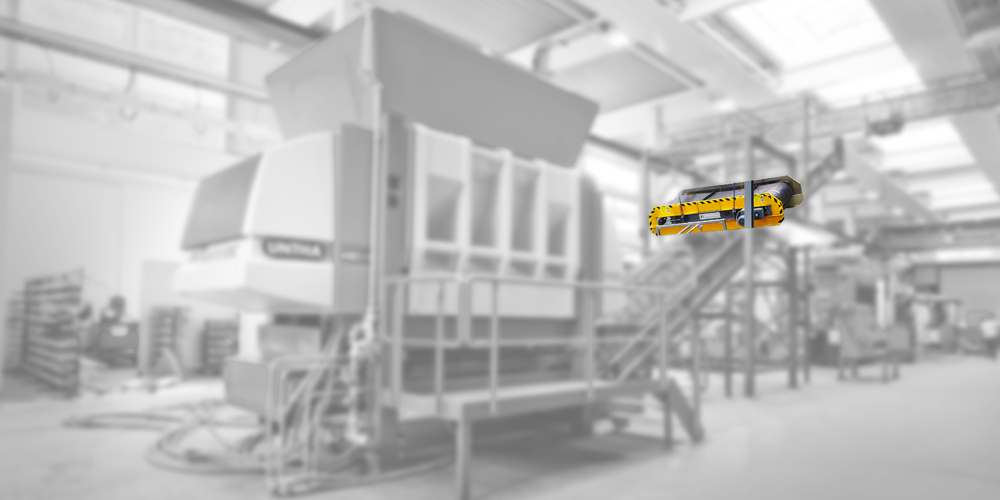
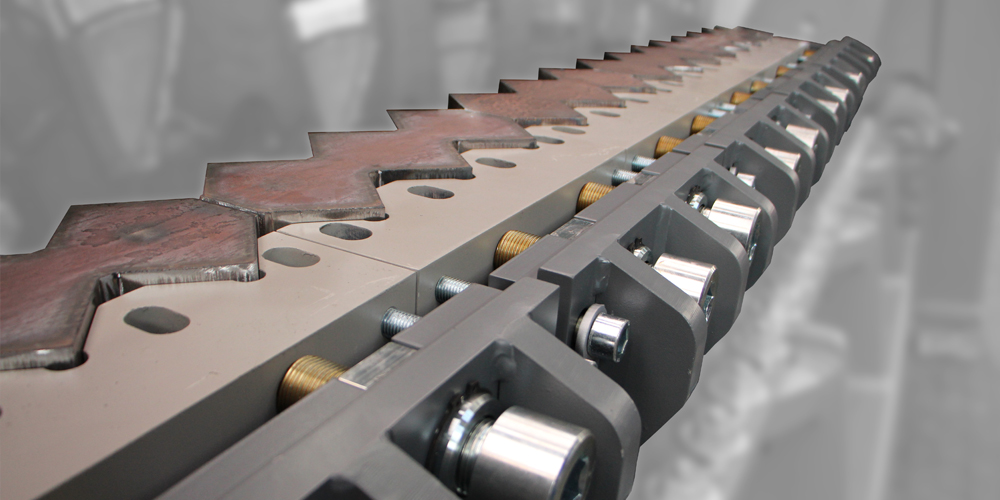
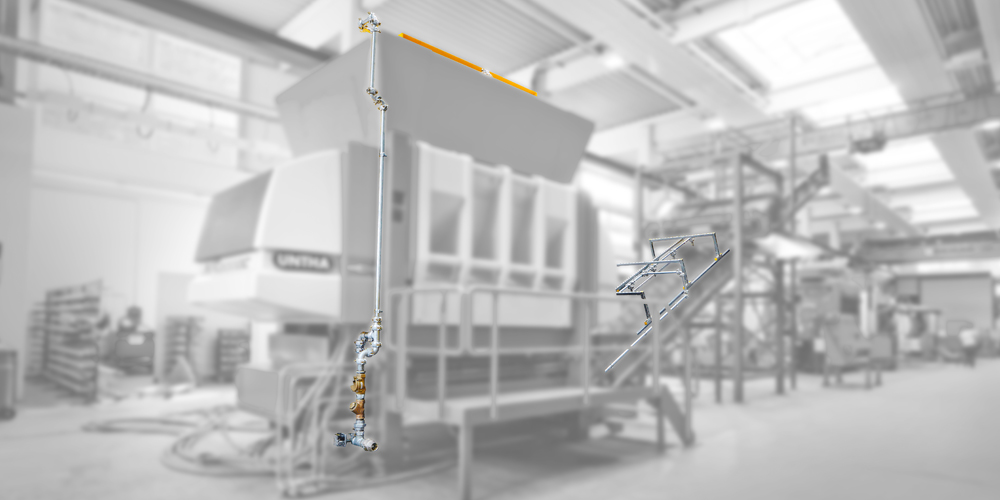
We offer different hopper shapes that are exactly adapted to your infeed type. Regardless of whether you need a hopper for a wheel bearing infeed or a hopper with a grabber infeed – we will always have a suitable solution available.